Maintenance and Repair 8 check valves 6″.
- Customer: NAMIN Co Ltd.
- Contractor: ORASCOM CONSTRUCTION
- End User: Upper Egypt Electricity Production Company.
- Site: New Assiut Power Plant.
Introduction :
The customer has eight check valves need a repair because they are leaking internally and affected on the plant performance. These valves are working in high pressure, high temperature and they are from special alloys.
We proposed two solutions:-
- Carrying out the repair activity out site but it needs to cut the valves to take these valves to our workshop which everything is available but cutting, welding and heat treatment process are costly and difficult.
- Doing the repair at site and we found a big problem that how to deal with the seat which is welded so we found the solution to manufacture a special tool which should be accurate and effective.
After discussion with our valued customers we have selected the second solution and start the work immediately.
To get the internal valve dimensions which unavailable, we went to the power plant and using accurate measurement tools to get dimensions at site from the existing valves.
During inspection and dimensions scanning we found that the seals and packing need to be replaced with new parts for some valves, we put accurate specification and get its dimensions also in order to source it from the specialist manufacturers of seals and packing which was delivered to the site before starting repairs according to our team defined specs and details drawings.
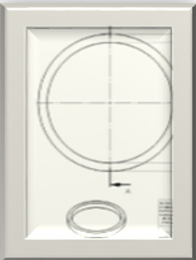
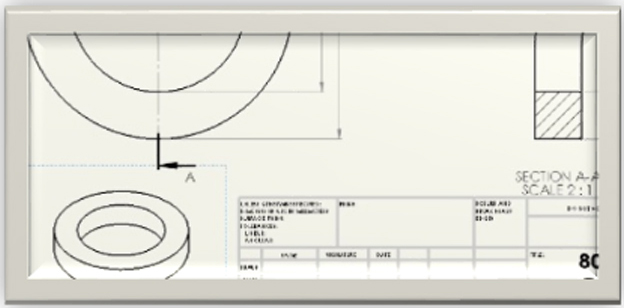
You can see also photos for the old seal and packing.
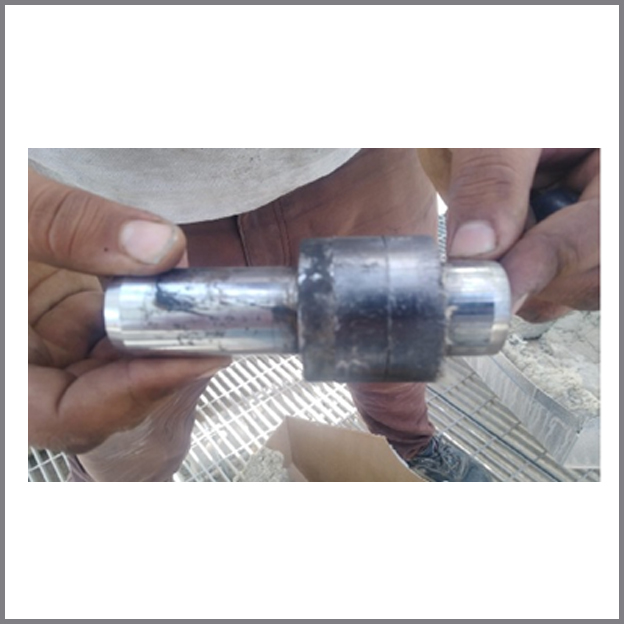
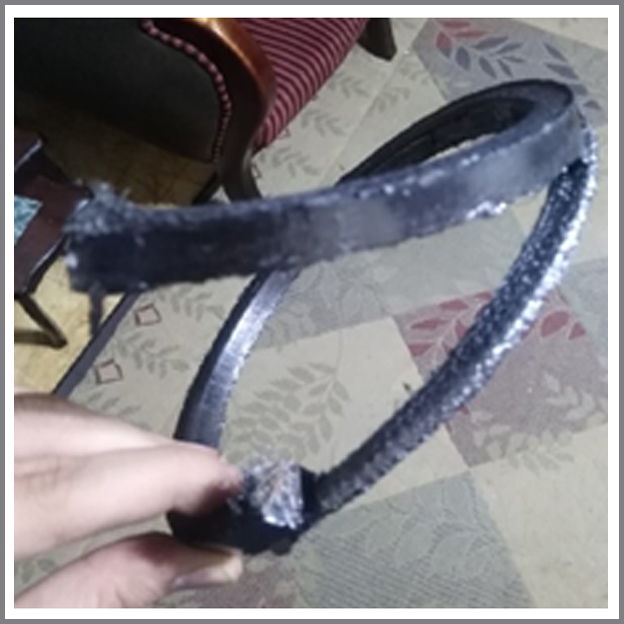
(2) Special tool manufacturing:
According to the existing dimension and site visit we start designing special tool to be suitable to the seat and very accurate because we will work at the plant which means there is no chance to try this tool so it should be ready for carrying work without any problems and in so accurate manner.
We spent more than 20 days to do this special tool and make sure that it is suitable for the seat at the site. See the following photo.
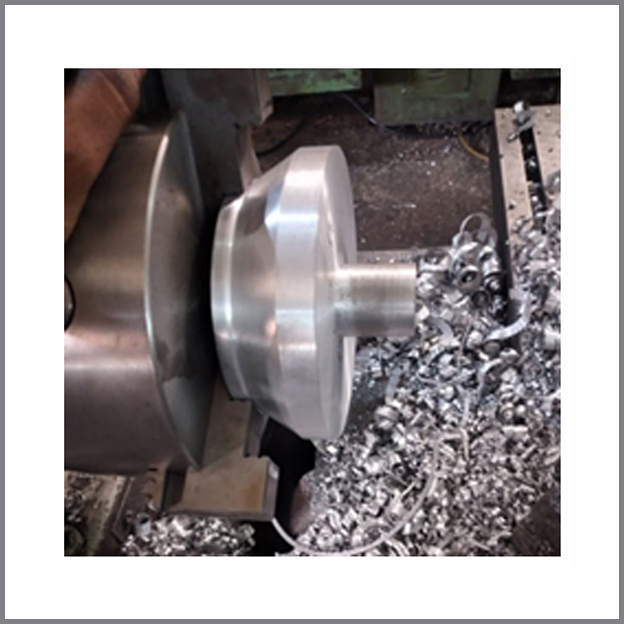
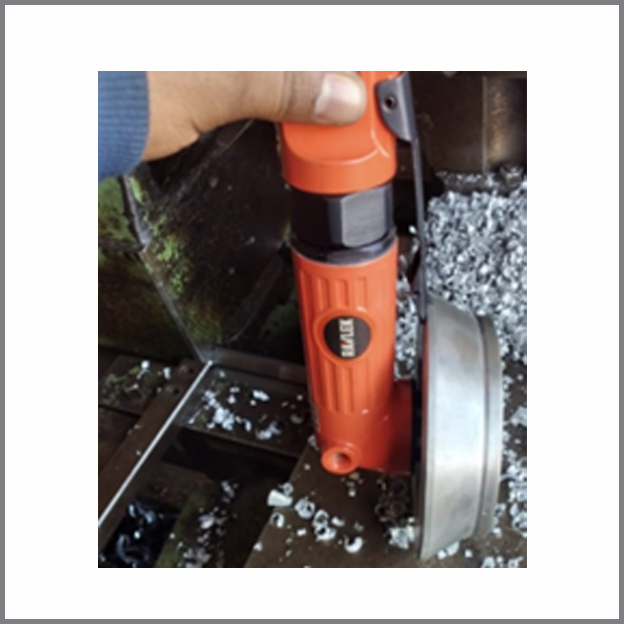
(3) The maintenance and repair activates:
We sent our qualified team consists of our engineer and technicians to finalize repair at site which was carried out under full supervision of power plant and customer experience representative who were satisfied of our professional work there.
Maintenance steps:
- Opening and dismantling valve.
- Valves incoming inspection and the results as mentioned in the following table and pictures:
Valve Pipe | Line Number | Seat | Disk | Pin Group |
Line | ||||
Have critical | Have critical | One of set | ||
1 | corrosion spot ,its | corrosion spot ,its | screw is | |
A | depth 0.1 mm | depth 0.1 mm | missing | |
shown as figure 1 | shown as figure 2 | |||
Slightly pitting and | Slightly pitting | One of set | ||
2 | corrosion spot | and corrosion spot | screw is | |
Shown as figure 3 | Shown as figure 4 | missing | ||
Slightly pitting and | Slightly pitting | No missing | ||
1 | corrosion spot | and corrosion spot | screws | |
B | Shown as figure 3 | Shown as figure 4 | ||
Slightly pitting and | Slightly pitting | One of set | ||
2 | corrosion spot | and corrosion spot | screw is | |
Shown as figure 3 | Shown as figure 4 | missing | ||
Slightly pitting and | Slightly pitting | One of set | ||
1 | corrosion spot | and corrosion spot | screw is | |
Shown as figure 5 | Shown as figure 6 | missing | ||
C | ||||
Slightly pitting and | Slightly pitting | Three of set | ||
2 | corrosion spot | and corrosion spot | screw are | |
Shown as figure 5 | Shown as figure 6 | missing | ||
Have critical | Have critical | One of set | ||
1 | corrosion spot ,its | corrosion spot ,its | screw is | |
D | depth 0.2 mm | depth 0.2 mm | missing | |
shown as figure 7 | shown as figure 8 | |||
Slightly pitting and | Slightly pitting | All the set | ||
2 | corrosion spot | and corrosion spot | screw are | |
Shown as figure 5 | Shown as figure 6 | missing | ||
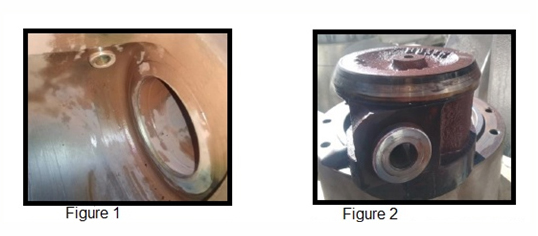
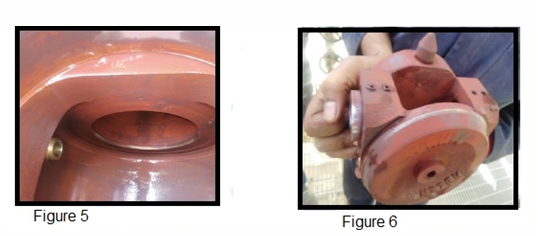
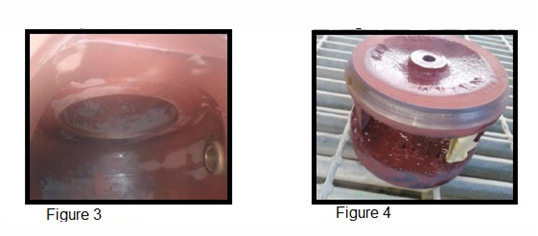
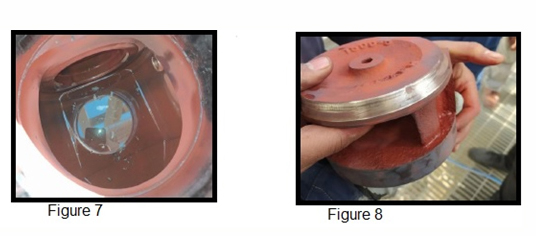
- 3) Turning the disk on a lath at workshop till became very fine face.
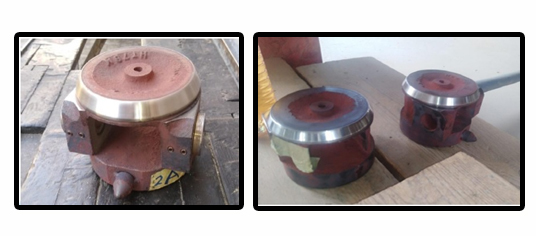
- 5) Perfect blue contact test of a disk and seat as shown:
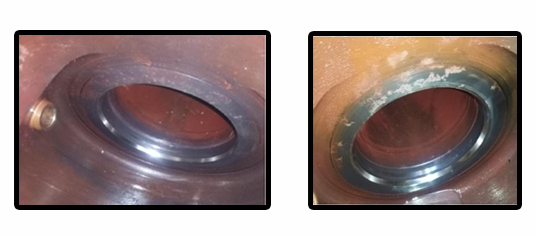
- 4) Grinding the seat at site using our special tool.
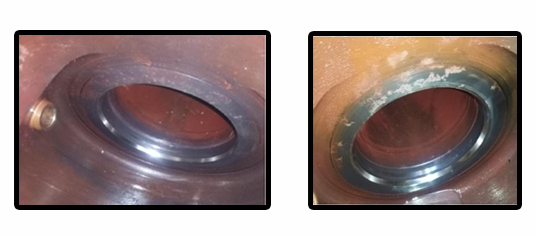
- 6) Reassembling the valve parts with full set screw and changing most of the packing and seal.
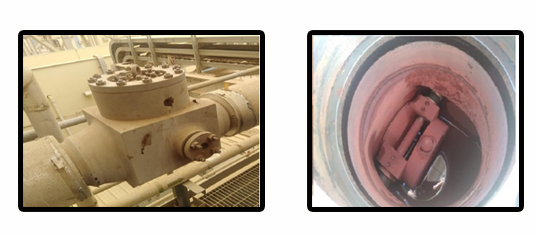
(4) Conclusion:
- After the above eight valves have been repaired we started the guarantee period for the valves as new units.
- We sent the customer the RCA for the valves with our recommendation for future operation.
NEGM ENERGY confirm our availability to support our customers to make sure the qualified operation and match with the target work requirements Electrical, Mechanical, Chemical, Instrumentation, Commissioning Services or Architecture Engineering.